Plastics Today
Spare Parts Team Lead in Europe also harvests a 200-tree orchard!
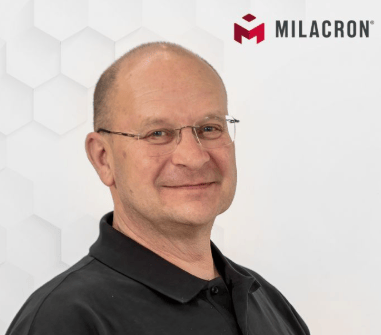
Dirk has been a valuable part of Milacron for 36 years, leading our parts team in Europe since 2023. With his expertise, he and his team ensure that our customers worldwide are supplied with the right components quickly and reliably.
At the age of 19, Dirk started in the warehouse of Klöckner Ferromatik (Ferromatik Milacron GmbH), where he became familiar with machine parts, and eventually transitioned to the customer service workshop where he executed customer repairs.
Since late 1990, Dirk has been a subject matter expert and primary contact person for Milacron customers in search of spare parts. He took over as team lead of our European spare parts team in 2023, where he prepares tailormade offers for customers, coordinates the processing of global spare parts requests, manages the order processing system, and oversees direct sales.
Family, Fun & Schnapps!
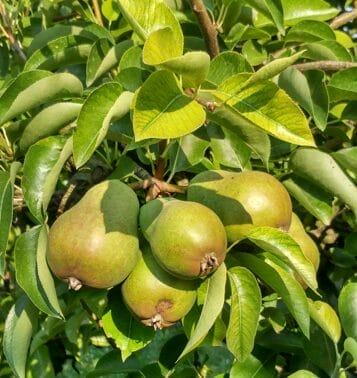
When he’s not at Milacron, Dirk keeps busy on his property with his wife of nearly 25 years, Doris, and their two grown sons – Nico (30) and Norman (22). They cultivate an orchard of nearly 200 pear trees for harvest through their very own distillery! Delicious pear schnapps and liqueurs are the product of their labor each season.
Dirk and his wife also enjoy visiting the nearby amusement park, Europa Park, and eating out with their sons (and their partners). The two look forward to being grandparents one day – family is truly everything to Dirk!


Operating in the plastics processing industry, we understand the critical role we play in shaping not just products, but also perspectives. While plastics are at the center of several end-market applications, we believe that environmental responsibility must evolve alongside industrial progress.
To celebrate World Environment Day, we recently took a step outside into our community to prove that sustainability begins with action. In a large-scale initiative by the Ahmedabad Municipal Corporation, we participated in the Sabarmati Clean Up Drive in collaboration with Drishti Foundation.
Over the course of the day, our team of 30 Milacron employees joined hands with fellow citizens to:
- Clear various kinds of waste from the riverbed
- Collect and safely dispose of numerous jumbo garbage bags filled with debris leaving the surroundings clean
- Raise awareness about sustaining this cleanliness through community engagement
To further nurture this spirit, we also distributed plant saplings to each participating employee – a living reminder that growth and change starts small but is meaningful throughout.
At the intersection of innovation and responsibility, we continue to champion solutions that drive a bigger purpose. Corporate responsibility stretches beyond business. By acting locally, we aim to contribute to the global call for sustainability.
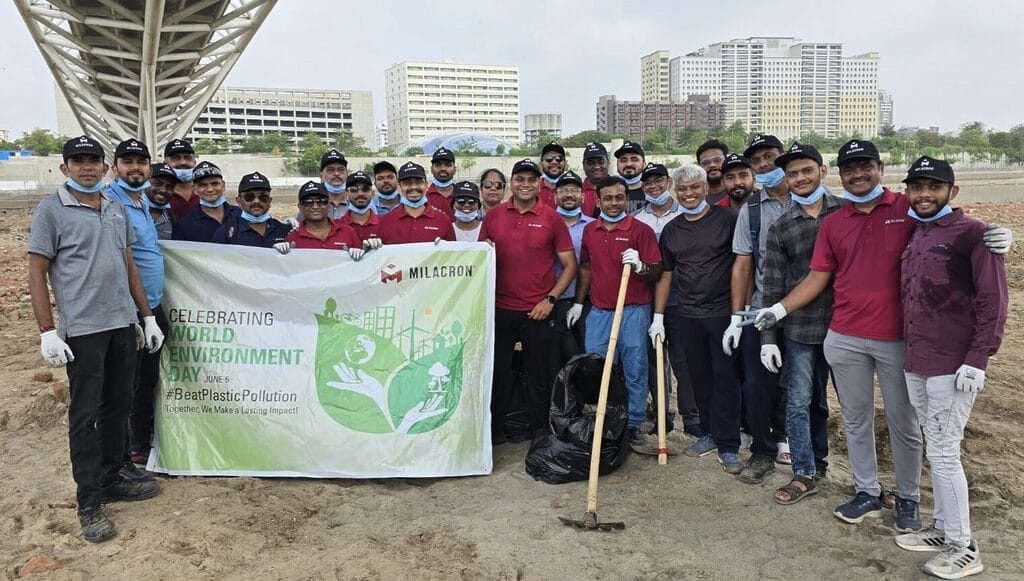
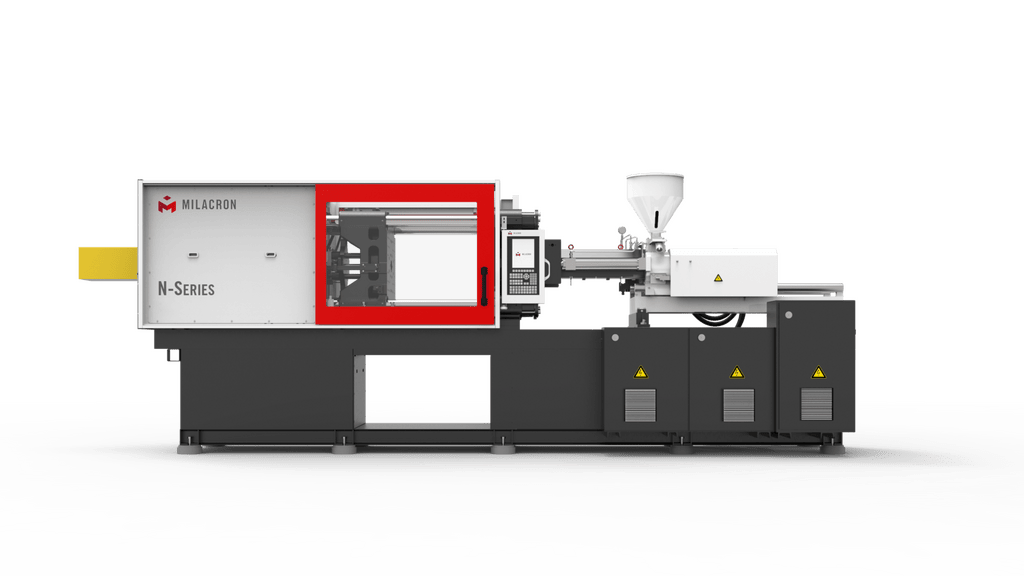
The plastics processing industry is undergoing unprecedented transformation, driven by evolving customer expectations, technological innovation, and a growing emphasis on sustainability. In today’s competitive environment, plastic processors must pursue higher productivity, lower energy consumption, and greater operational reliability — all without compromising manufacturing goals.
At Milacron, we believe that innovation must be practical, measurable, and future-proof. By combining deep industry expertise with real-world validation, we continue to empower plastic processors to address emerging challenges with greater agility and assurance.
The Challenge: Balancing Efficiency and Productivity
Today, manufacturers face a dual imperative: increasing throughput while minimizing operational costs. Historically, these goals often competed, but advances in machine design, control systems, and intelligent operating modes make it possible to achieve both simultaneously.
With energy costs, machine downtime, and maintenance-related disruptions posing significant operational risks, selecting the right technology platform has become a strategic decision influencing long-term competitiveness and profitability.
A Smarter Approach: Optimizing Efficiency Through Innovation
Recent comparative evaluations highlight how next-generation injection molding solutions deliver tangible improvements across key performance metrics. Real-world validation ensures that technological advancements translate into measurable outcomes on the shop floor.
For example, smart injection molding machines have demonstrated the ability to:
- Achieve up to 20% higher energy efficiency, depending on duty cycle & utilization, significantly reducing power consumption and operating expenses.
- Deliver up to 3% higher productivity, resulting in thousands of additional cycles per year and increased annual throughput.
- Maintain superior clamp stability and minimize vibration, extending machine and component life while enhancing operational consistency.
These advancements reduce the cost per part and contribute to more sustainable manufacturing practices — a priority that continues to gain importance across industries.
Milacron’s Perspective: Setting New Benchmarks in the Small Tonnage Injection Molding Solutions
At Milacron, we are committed to engineering solutions that deliver measurable value for plastics processors. Through rigorous head-to-head testing against comparable competitor models, the new N-Series, equipped with the Mode Switch Feature, ranging from 110 to 220 Tons, has set new benchmarks for efficiency, productivity, and reliability.
Operating in Eco Mode*, the N-Series helped achieve the following:
- 8% greater energy efficiency, saving approximately 2,900 kWh annually.
- 3% higher productivity, generating around 46,000 additional cycles per year.
- 50% lower vibration levels, promoting smoother operations and longer equipment life.
By offering flexible operating modes — from Eco Mode* for energy savings to Performance Mode for maximum throughput — the N-Series enables manufacturers to dynamically optimize their production strategies without compromising operational excellence.
Designed to meet the needs of diverse sectors, including Automotive, Packaging, Consumer Goods, Construction, Medical, Electrical, Electronics, and Telecommunication, the N-Series emerges as the new benchmark in small-tonnage injection molding solutions.
*Patent Pending
Conclusion
As the plastics processing industry evolves, the demand for innovative, energy-efficient, and resilient plastic processing solutions will continue accelerating.
At Milacron, we remain dedicated to driving this transformation by blending technological innovation with real-world validation. Through highly engineered solutions like the N-Series, we aim to empower manufacturers to achieve greater operational excellence, enhance sustainability, and confidently lead into the future.
Abstract
Manufacturers are turning to more innovative, data-driven machinery solutions as the plastics processing industry faces increasing demands for efficiency, sustainability, and operational reliability. This article explores how technological advancements enable processors to achieve higher productivity and lower energy consumption without trade-offs. It highlights key industry trends and presents insights from Milacron’s real-world validation of the N-Series 150T, a next-generation injection molding machine engineered for measurable performance gains.
By blending innovation with practical outcomes, Milacron is helping manufacturers navigate evolving challenges and drive transformative success.
Key Takeaways
- Emerging Trends: Technological advancements in injection molding enable plastic processors to achieve higher energy efficiency, improved productivity, and greater operational reliability.
- Real-World Validation: Milacron’s N-Series 150 demonstrated measurable performance advantages, including 8% higher energy efficiency, 3% increased productivity, and 50% lower vibration compared to a comparable competitor model.
- Future-Ready Solutions: By combining flexible operating modes and more innovative design, Milacron empowers manufacturers to optimize production strategies and enhance long-term sustainability in a competitive marketplace.
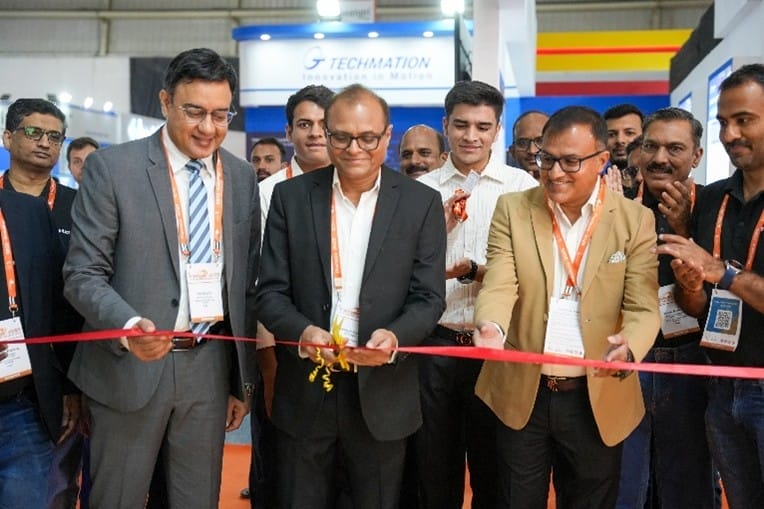
As one of the leaders of the plastics processing industry, Milacron India made a commendable presence at Plastasia 2025 – a four-day event that brought together pioneers, partners, and professionals from across the polymers sector. Our participation was strategic and substantial, with a dual presence at our own stall space and at our partner’s booth, both powered by our flagship injection molding machines.
Setting the Stage: A Grand Opening and an Insightful Address
The first day of the exhibition commenced with a formal inauguration ceremony, where our esteemed guest, Mr. Santosh Kumar Chhajer, Director, Dev Packaging, cut the ribbon to mark the beginning of an exciting show. This was followed by a keynote address by Mr. Bill Shukla, Managing Director, Milacron India, who emphasized our commitment to transforming plastic processing through innovative solutions.
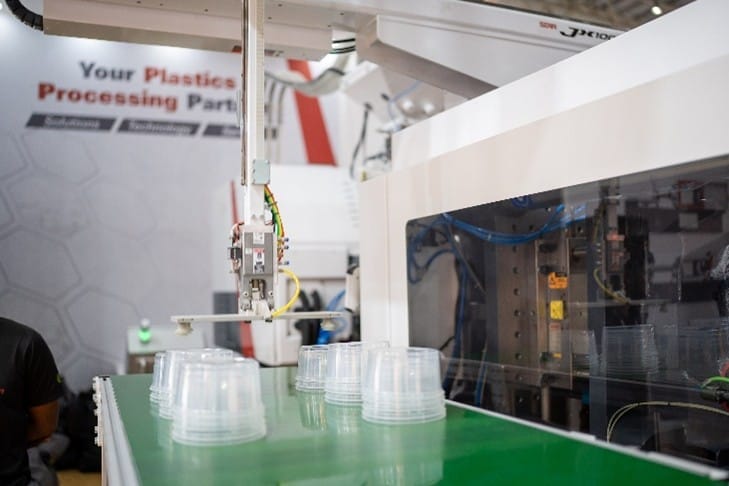
Meanwhile, visitors were enthralled by our all-electric eQ 280 producing 1000ml containers live, showcasing both efficiency and precision in real-time production.
We recorded an impressive footfall on the first day itself, marking a dynamic beginning to the event and setting the stage for more engaging interactions with industry professionals.
Building Momentum with Engineering Excellence
Keeping the energy intact, we moved on to the next day, engaging with several visitors and talking about our diverse range of solutions. From micro to large-part molding machines, we presented our portfolio of machines suited for various end-market applications.
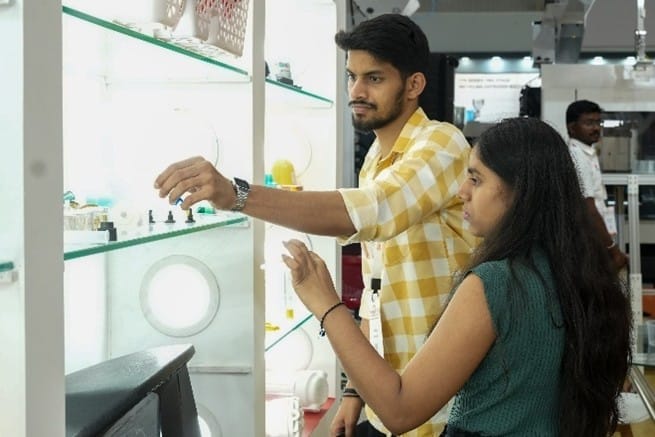
Our team of sales and service professionals collaborated with subject matter experts to talk about some of our flagship technology, including our low-pressure injection molding solutions.
We also made sure to dedicate a separate section of our booth for M-Powered – our suite of IIoT solutions that runs sophisticated algorithms that utilize real-time machine learning to monitor machine operations.
Sustained Interest, Steady Impact
Day 3 witnessed continued enthusiasm at our booth as we welcomed visitors from all over the country who marveled at our all-electric eQ 280’s lightning-fast injection molding abilities. Our team remained engaged throughout the day at both stalls – ours and our partner’s – delivering expert guidance and addressing technical queries with clarity.
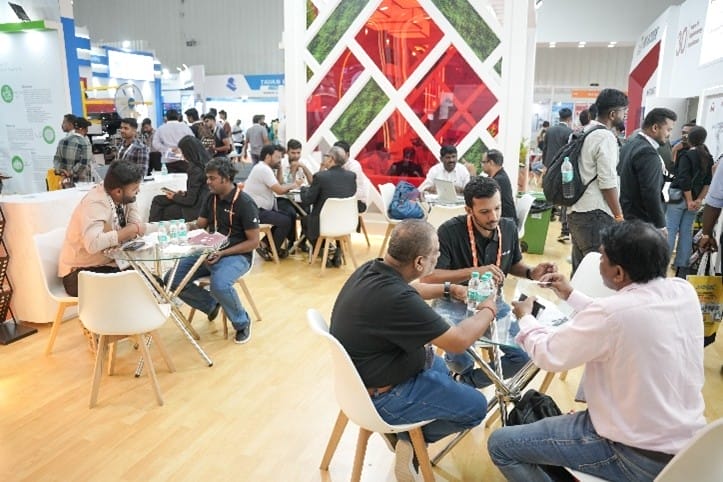
For many visitors, this day served as a valuable opportunity to connect with our team and witness our solutions beyond the initial buzz. This steady momentum was an affirmation towards our position as a trusted plastics processing partner driven by innovation.
Marking A Resounding Success
We brought the last day of the exhibition to a close with enthusiasm and significant impact. Across four days, we recorded over 1500 visitors, fielded numerous enquiries, and secured multiple customer registrations.
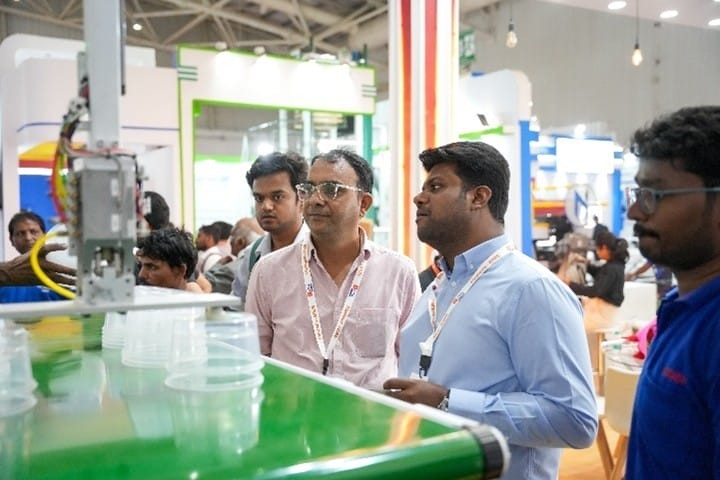
From live production of 1000ml food containers to powerful conversations with industry leaders, our presence at Plastasia 2025 underscored our role as a future-ready plastics processing partner.
We also concluded the exhibition on a high note, as we were crowned Best Stall at Plastasia 2025 – a recognition of our immersive, engaging, and technically-driven showcase. This award was a testament to our mindful design and impactful storytelling delivered across our exhibit.
Thank You Note
Driving Growth through Innovation and Operational Excellence
We extend our sincere thanks to every visitor and fellow industry professional who visited us at Plastasia 2025. Your sustained interest, insights, and enthusiasm made our four-day showcase truly memorable.
While the exhibition has come to an end, our collaboration doesn’t stop here. This experience reaffirmed our commitment towards innovation, engineering excellence, and supporting our customers with solutions, technology, and services. We move forward with stronger connections and renewed momentum.


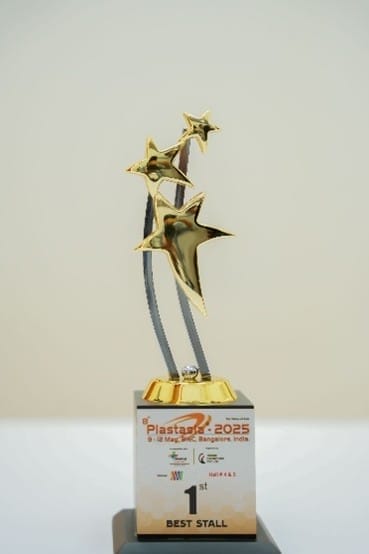
A part-time firefighter, the CNC Mill Machine Operator of 36 years lives life to the fullest!

A community hero and machine operator don’t often go hand-in-hand, but that’s just another day in the life of Milacron’s Matt Williams.
He’s humble, and helpful, and likes a good challenge.
Matt first laid down his Milacron roots at the former Wilmington, Ohio plant in 1988. It wasn’t too far from home and the company seemed to be a good fit for a young man that enjoyed working with his hands.
Today, 36 years later, Matt puts his extensive experience to productive use as a CNC Mill Machine Operator at the company’s Mount Orab, Ohio screw and barrel manufacturing facility located only 10 minutes from the global headquarters.
During his Milacron tenure, Matt has had the opportunity to run various machines. Barrel cell machine operations, and his current machine centers position, rank among his favorite roles to-date in plastics processing manufacturing.
A man that wears many hats in a week’s time, Matt’s service doesn’t end when his day is done at Milacron. Closer to home, he serves as a part-time firefighter for the Washington Court House Fire Department – a role that delivers both passion and purpose. Then finally, he may get the chance to unwind a bit with a hobby he’s grown quite fond of – woodworking.
Matt lives in Washington Court House, Ohio with his wife, and takes great pride in his two grown kids, as well as his role as “grandpa” to three outstanding grandchildren.

————————————————
Thank you, Matt, for your 36 years of service to our organization, as well as for putting your own life on the line for others in the field of public service.
Grinder Operator out of McPherson, Kansas dedicates more than three decades to Milacron!
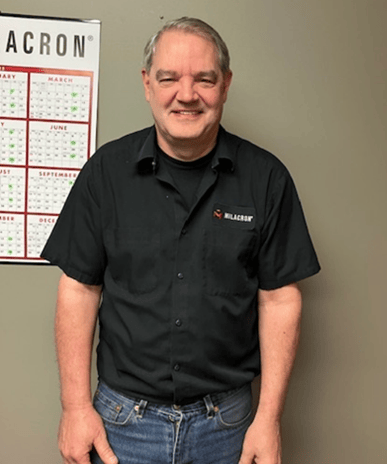
More than three decades ago, Jeff Unruh was working for a construction company, and a contact at that company introduced him to Milacron. The rest of his career story is exactly that – HIStory!
Upon arriving at Milacron in November of 1992, Jeff spent the first five years in Pre-Inspection, and from there moved into a grinder role. He’s worked on the same machine at the McPherson, Kansas manufacturing operations facility for the last 28 years – truly a subject matter expert grinder!
Family
A native of Topeka, Kansas, Jeff came to McPherson through the construction company that he worked for prior to getting hired on with Milacron. He met his wife of 37 years in McPherson, where they’ve lived ever since raising their three daughters, alongside now three sons-in-law, and three grandchildren.
Hobbies
When he’s not at Milacron grinding away on his favorite machine, Jeff enjoys woodworking and doing projects for his grandchildren. He also enjoys traveling with his wife and vacationing with his daughters and their families.
Thank you, Jeff, for taking a chance on Milacron more than 30 years ago! We couldn’t be more thankful for your expertise, positive attitude, and willingness to serve the plastics processing industry with passion and purpose year-in-and-year-out.
Plastics News
A Prestigious Industry Recognition and a Moment of Pride for Milacron Associates and Partners!
Milacron is proud to be recognized as one of the ‘Best Plastics & Polymers Brands 2025’ by ET Now Polymers and the Times Group—a prestigious acknowledgment of our commitment to innovation, technology, and service excellence in the Indian plastics and polymers industry.
A Legacy of Innovation & Excellence
For decades, Milacron has been more than a brand—it has been a pioneer in shaping the evolution of plastics processing technology. With a strong presence in India and beyond, Milacron India has powered industries with:
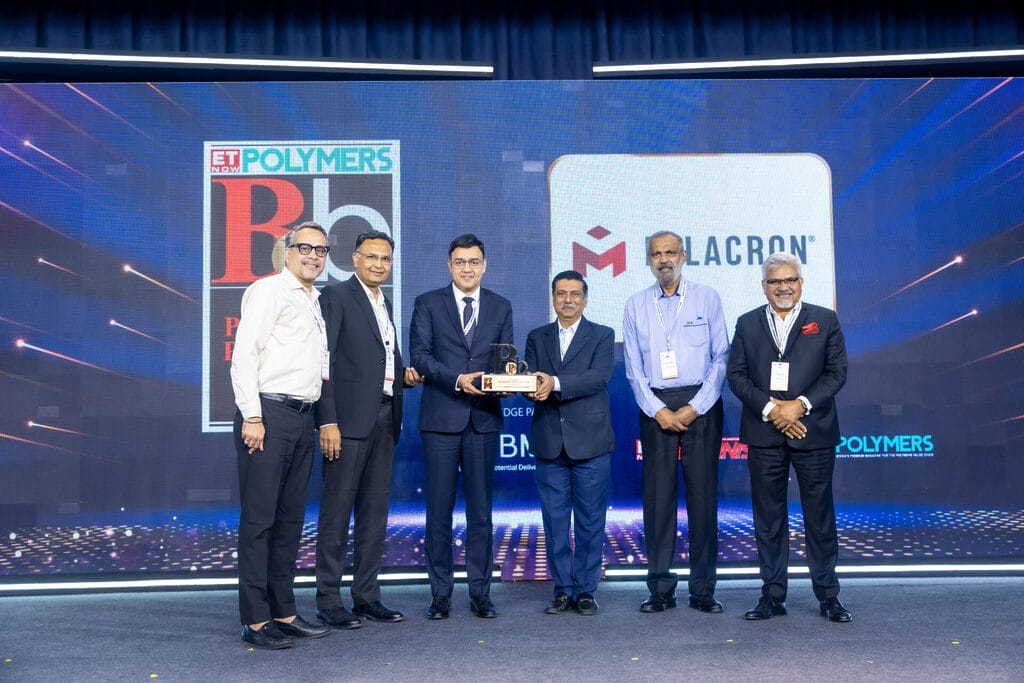
✅27,000+ indigenous machines, driving operational excellence
✅Cutting-edge technology that advances plastics manufacturing
✅A relentless commitment to sustainability and innovation
A Recognition That Inspires the Future
This achievement is a shared success—a result of the dedication, expertise, and passion of every Milacron associate. It reinforces our standing as a pioneering force in the industry, pushing the boundaries of what’s possible in plastics processing.
At the felicitation ceremony, our Managing Director, Mr. Bill Shukla, reflected on Milacron’s journey, future aspirations, and the role of innovation in advancing sustainable manufacturing. He also participated in a panel discussion on “Crafting India’s Future: Advancing Innovation, Skill, and Sustainability in Manufacturing,” sharing insights on how technology is shaping the next era of plastics and polymers.
What’s Next?
As we celebrate this milestone, we remain committed to innovation, sustainability, and delivering customer success. This honor is not just a reflection of our past achievements but a motivation to set new benchmarks in the global market.
Here’s to many more milestones ahead!
Anticipated growth acceleration further strengthens Milacron’s position as the largest North American-based original equipment manufacturer of its kind with a dynamic global footprint.
[BATAVIA, OHIO] March 31, 2025 – Bain Capital, a leading private investment firm, today completed the majority investment in Milacron (or the “Company”), a global industrial leader in the manufacture and distribution of highly-engineered injection molding, extrusion solutions, and aftermarket services for the plastics processing market. Bain Capital will partner with Milacron’s current owner, Hillenbrand, Inc. (NYSE: HI), which will remain a significant investor in the business to ensure the Company’s continued growth.
Milacron has built a legacy over the past nearly 60 years that is defined by innovation, expertise, and a deep commitment to serving its 27,000+ customers as well as each of its nearly 2,000 associates worldwide.
“This is an exciting step in the next chapter for Milacron,” said Mac Jones, CEO of Milacron. “We have established a solid foundation of serving plastics processing customers around the globe for more than five decades through innovative technologies, solutions, and service. More focused resources will allow for the continued development of our offering and the ability to respond to our customers’ needs more readily, enhancing their missions and sustaining their continued success.”
The diverse range of industry end-markets serviced by Milacron includes automotive, construction, consumer goods, electronics, medical, telecommunications, packaging, and much more. The original equipment provider of plastics manufacturing solutions is the largest US-owned and globally served of its kind, with regional offices in Asia, Europe, and Latin America.
“This is a pivotal moment in Milacron’s 50-year history—an opportunity to build on its legacy of innovation and service to accelerate growth,” said Matt Evans, Partner at Bain Capital. “Together, we share a vision for long-term success, driven by strategic investments in technology, products, and services that enhance value for customers in the U.S. and around the world. We are excited to partner with the Milacron team to strengthen its foundation and create lasting impact globally.”