Plastics Today
A collaboration in large-part plastics sustainability through structural foam molding innovation
For nearly three decades, ORBIS Corporation has turned to Milacron’s industry-leading low-pressure injection molding (LPIM) capabilities to meet its customers’ plastics processing goals, and for good reason – Milacron has more than 50 years in the LPIM business.
Today, the Milacron L-Series platform of machines comprises one-third of ORBIS’s fleet of IMMs with units deployed at five North American facilities – a collaboration that benefits ORBIS through lightweighting, reduced scrap, the ability to utilize up to 100% regrind flake material during production, and increased machine efficiency.
Conversely, Milacron has relied on ORBIS to trial various innovations in plastics and conduct machine retrofits throughout the nearly three decades the two have been in collaboration. In addition, ORBIS became a beta site for the Cincinnati-based OEM’s IIoT remote monitoring solution that’s now integrated into every new Milacron injection molding machine installed for plastics processors across the U.S. and Europe.
“Milacron continuously provides us with better technologies, which allow us to continue to improve our efficiencies,” said Lynn Hediger, Vice President of Product Management for ORBIS. “Essentially, we can get more pieces out the door per hour, thanks to Milacron’s L-Series LPIM technology.”
ORBIS has been in plastics for nearly 70 years and is an industry leader in injection-molded reusable packaging. Today, their products are used in a wide variety of industries, including automotive, grocery, pharmaceutical, e-commerce, automated warehouses, and many others. Designed for long service life, their reusable packaging products replace single-use boxes and wooden pallets and can be recycled at the end of their life.
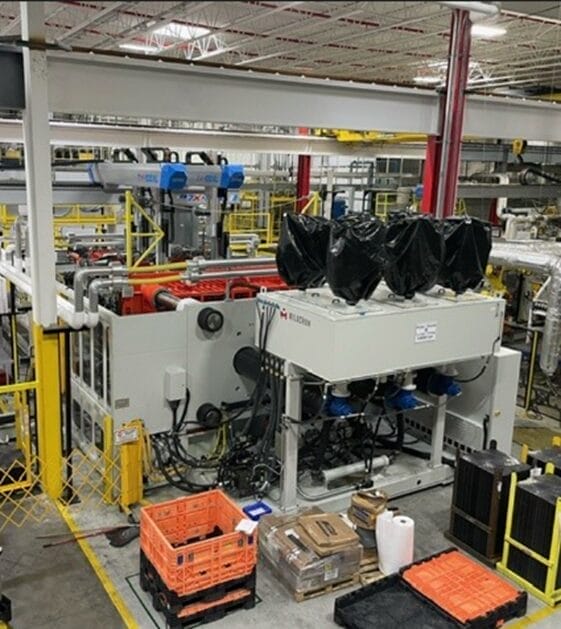
According to the ORBIS website (orbiscorporation.com), the company’s goal is to collaborate and facilitate a more sustainable way for its customers to move and protect goods in the supply chain. “We analyze your business to design and execute an integrated reusable packaging program that increases your efficiency while reducing your environmental impact.”
Milacron’s LPIM structural foam technology is ideal for molding ultra-large and thicker plastic parts – this combination of a solid surface over a cellular-foamed core results in a high strength-to-weight ratio. Through this lightweight technology, the Milacron L-Series LPIM platform provides partners like ORBIS the capability of producing large-part plastics with thicker wall sections and detailed part designs at a lower material weight.
“With Milacron’s LPIM machine platform, ORBIS is positioned to support sustainability initiatives driven by customers due to our continuous improvement mindset and eagerness to make more sustainable and efficient products,” said Hediger. “Not only can we achieve higher recycled material content in our products, but we also leverage opportunities to lightweight and improve packaging efficiency for our customers’ transportation loops,” he said.
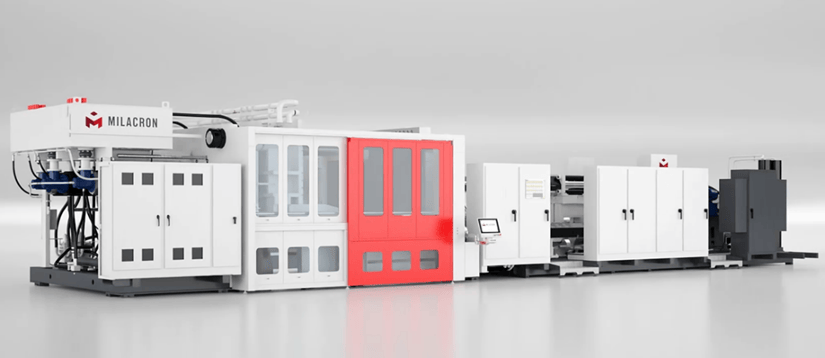
The evolution of a sustainable collaboration
ORBIS bought its first LPIM machine from a Milacron-acquired OEM in the mid-nineties. Improved efficiency was a primary goal back then and seeing as though Milacron had been at the forefront of LPIM advancements since the 1970s, it was an advantageous fit. Since that time, corporations have begun integrating sustainability efforts into their Corporate Social Responsibility models, including ORBIS customers.
“Operationally, Milacron has helped ORBIS reduce scrap, avoid the need for re-compounding recycled materials, and increase our press uptime,” said Nathan Marret, Senior Director of Molding Operations for ORBIS. “This has delivered us an advantageous market position that supports our ongoing commitment to efficiency, sustainability, and quality for our customers.”
The scrap material produced by ORBIS, along with end-of-life products purchased back from customers, is reground and fed right back into the Milacron machines, instead of having to first put it through the compounding process. This results in energy savings which additionally benefits ORBIS customers.
“Our reusables are designed for long service life and are intended to replace single-use boxes and wooden pallets in the supply chain,” said Hediger. “By design, reusable totes, pallets, dunnage, metal racks, and bulk systems are used repeatedly during their service life. And, at the end of their life, they can be recovered, recycled, and reprocessed into new packaging products without entering the solid waste stream.”
Over the last three years, Marret says ORBIS has particularly relied on Milacron’s advanced LPIM technology for its automotive industry customers, whose stakeholders tend to hold them to higher standards. He says the EcoVadis sustainability rating platform is now an elevated priority for many ORBIS customers.
“Our automotive customers want to ensure their stakeholders see the ‘real sustainability’ efforts being made,” explained Marret. “The EcoVadis score is what they use to report out on sustainability, so in turn, they are asking their suppliers to use this too.”
EcoVadis rates businesses’ sustainability based on environmental impact, labor, ethics, and procurement practices. According to its website, EcoVadis serves to help companies manage environmental risk and improve sustainability across their supply chains, as well as comply with global regulations.
Part of the data that feeds an EcoVadis score on environmental impact in the plastics industry is the amount of regrind material utilized in part production, as well as overall energy reduction, both of which Milacron LPIM technology affords ORBIS for their customers, according to Marret.
He estimates other large industry sectors within the ORBIS customer base will also soon utilize the EcoVadis sustainability scorecard – and, when they do, ORBIS is ready and willing to support all its customers to ensure sustainability requirements are met accordingly.
“All of the steps we are taking in our sustainability measures within our packaging are in line with EcoVadis,” he said.
ORBIS utilized as a beta for Milacron IIoT solution
ORBIS may consider the effective and efficient production of reusables for its customers its principal priority, but the overall performance of its fleet, or OEE, is also critical – downtime is costly in this industry.
ORBIS first became a beta site for Milacron’s remote IIoT solution, M-Powered, on its high-pressure injection molding machines back in 2016 to monitor its machines and their related processes. Since then, Milacron has helped ORBIS build baseline predictive analytics that the company uses to plan repairs and maintenance, as well as to troubleshoot.
M-Powered turns Milacron machine data into valuable insights that provide ORBIS with unique machine intelligence. These real-time files are collected, combined, and analyzed to help the ORBIS team prevent or reduce inefficiencies.
“Milacron’s M-Powered has provided us the insight to take machines down mindfully for proactive part replacement versus waiting for a catastrophic failure to occur,” said Hediger.
ORBIS integrated M-Powered into its Milacron L-Series machine platform earlier this year. The processor appreciates M-Powered’s ability to improve its machine reliability and press uptime, but most notably its efficiency in predicting failures in advance.
Through this digital monitoring solution, the ORBIS team can tap into Milacron Engineering talent, as well as remote troubleshoot without having to wait for a technician, which equates to machine uptime.
“This is where M-Powered benefits us most,” said Marret. “We oftentimes only have to wait a matter of hours to get problems identified, versus days.”
Milacron customers see sustainability increase through trackable scrap reduction, better energy efficiency performance, and reduced overall risk on their machines.* It’s considered such an advantageous value proposition for customers that Milacron now integrates M-Powered onto all its new machines in the U.S. and Europe for free for the first 12 months of ownership.
A collaborative effort that drives efficiencies
As ORBIS awaits delivery of its latest Milacron LPIM machine that will operate out of the corporation’s Bardstown, Kentucky facility, orders continue to roll in from their customers. The company looks forward to continued growth with Milacron.
“ORBIS and Milacron have a strong bond in our similar vision,” he said. “We look at this as a long-term partnership – not just transactional.”
Additionally, Hediger said there is growth potential for ORBIS through the management of packaging for their customers. Essentially, the greatest sectors for growth will come from ORBIS customers who re-utilize packaging to its fullest potential and continue to grow through evolving sustainability measures.
“ORBIS wants to be on the forefront leading the industry in new technology and advancements in sustainable packaging for our customers,” he said. “We’re always looking for ways to expand and improve our operations. And, we will look to drive continued efficiencies in these operations with Milacron.”
*In October 2022, a Plastics News scrap reduction study reported the industry average scrap rate to be 3 to 4 percent. A top-tier Milacron customer in that same year reduced its scrap from 23% to under 1% with 42 machines running on M-Powered. In 2022, another Milacron M-Powered adopter saw an elimination of 7,000 hours of unplanned downtime on 22 machines in the first year of service. Yet another customer using M-Powered predictive analytics reported saving more than 18,000 kWh over the 12-month test period, while simultaneously producing 3,000 more parts. Milacron also proved to reduce carbon emissions and increase employee safety with M-Powered. Data analytics uncovered that customers used 1600 remote sessions in 2022. Of these sessions, M-Powered afforded customers a 50% solve rate, equating to a reduction of 800 service tech trips to customer locations and increased employee safety by not physically being at the machine to investigate issues.
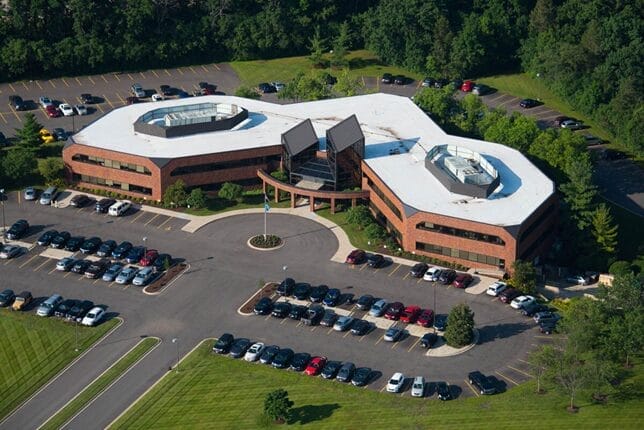
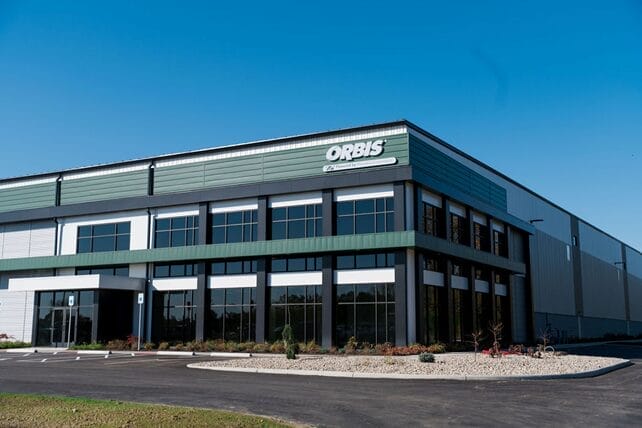
A new universal injection molding platform, progressive co-injection technology, an 85-foot extruder line with live cobot demonstrations, in-mold foil decorations, exclusive IIoT digital solutions, and more on display this May.
[BATAVIA, OH] March 29, 2024 –Milacron®, a global leader in the manufacture, distribution, and service of highly engineered and customized systems within the plastic processing industry, will demonstrate advanced equipment solutions, innovative mold technologies, and comprehensive service and support systems at NPE May 6-10 in Orlando.
A pioneer in the plastics processing industry, and one of the largest North American-based OEMs, Milacron is set to showcase its latest advancements and innovative solutions, including the North American debut of its new M-Series IMM platform that features the largest clamp stroke available as standard in the mid-tonnage hybrid range within a compact footprint. Powered by industry-leading Fanuc motors and drives, the M-Series machines’ versatility and performance are designed to meet the demanding needs of global industries, from automotive and consumer goods to packaging and custom molders.
Booth W1601, the largest exhibit space at NPE 2024, is designed to offer attendees an array of plastics processing technologies. In addition to its M-Series machine line, Milacron’s showcase includes several work cells and industry-leading exhibits, alongside innovations from fellow Hillenbrand Operating Companies Coperion, DME, Herbold, Mold-Masters, and Rotex.
“Much has evolved in the plastics processing space since we were all last together at NPE 2018, including our integration into the Hillenbrand family of leading industrial brands,” said Mac Jones, Milacron President. “Our sizeable presence at NPE 2024 underscores Milacron’s drive to deliver solutions that Shape What Matters For Tomorrow™ in the plastics processing industry.”
Two different M-Series machine applications are planned for the booth. The M-1070, featuring Mold-Masters co-injection technology, is a two-cavity-mold pail application with up to 50% recycled core and includes IML (In-Mold Labeling) automation. The M-500 machine cell features a Mold-Masters hot runner and Kurz in-mold decoration technology for custom textures and backlit applications in global automotive and appliance applications.
The L-Series, Milacron’s LPIM platform, has been at the forefront of the low-pressure injection market for more than fifty years. Wide-range molding flexibility and part design are possible through nozzle sequencing. Most notably, the Milacron LPIM machine can run up to 100% regrind flake material, resulting in significant energy and resource savings. This commitment to sustainability offers a competitive advantage to customers in a world increasingly seeking to meet environmental compliance. Due to space constraints, the L-Series will not be featured at the show, but an in-booth animation loop will display the benefits of this industry-leading low-pressure IMM technology for large-part production in structural foam and structural web applications.
Several variations of Milacron’s durable, general-purpose, high-performance Q-Series platform will be present. The Q-Series features a double-toggle design that leverages a servo-hydraulic package delivering quality parts at a rapid pace while minimizing energy use. At the Milacron booth, the Q-170 machine displays a new G3 Mosaic control, DME mold technologies utilizing a bio-resin material, as well as custom ID/serialization and QR code stamping. A mobile phone holder will be the Q-170’s featured application. Additionally, Milacron’s Q-125 will be active in the Sepro booth (W143), where four private-labeled Sepro robots will integrate with the machine to produce a two-cavity mini disc.
The all-electric Fanuc Roboshot showcases two different applications within the booth that integrate DME Flosense water manifold technology. The Robo 55 features LSR (liquid silicon rubber) material and automation that is common in automotive, electrical, and medical applications. The cell includes a micro-plunger to precisely control small-capacity volume for the umbrella part produced that requires a tiny shot. Also in the booth, the Robo 275 machine cell shows a 48-cavity medical vial application. Partnering Operating Company, Mold-Masters, displays its new M3 thermocouple technology in this machine, ensuring precise temperature measurement in its Master-Series Pico hot runner with the Accu-Valve MX gate system. An added solution to this cell that makes it ideal for processors requiring a clean room environment, Milacron’s stainless steel water system is also featured on the Robo 275.At the far end of the cell, a platen-mounted robot with a conveyor retrieves the small plastic parts and places them in bins in a space-saving envelope containment area.
Milacron’s SG-75 extrusion pipeline exhibit can’t be missed, spanning more than 85 feet long, with an exclusive new control that fully integrates all line components. Additional features include the gravimetric feeder system, new polyolefin pipe heads, the latest technology in single/twin screws and barrels, dynamic downstream equipment, and post-production automation. Attendees can view an articulating 6-axis cobot technology at work through live demonstrations.
Lastly, show participants can interact with Milacron’s M-Powered digital IIoT solution. A portfolio of easy-to-use observational, analytical, and support services that provide customers with a competitive advantage, improved OEE, and reduced scrap rates, M-Powered leverages IIoT technology through sophisticated algorithms that utilize real-time machine learning to monitor machine operations. Milacron integrates M-Powered onto all its new machines in the U.S. and Europe for free for the first 12 months of ownership.
An innovative world leader in plastic processing, Milacron delivers the next generation of manufacturing technology this May for a wide array of industries. From a new IMM platform in the mid-tonnage range to the largest extrusion line the company has ever exhibited, Milacron partners at NPE 2024 with fellow Hillenbrand Operating Companies, as well as some of the top plastics processing partners in the industry, to Shape What Matters For Tomorrow.
About Milacron
Milacron (www.milacron.com) is a global industry and technology leader in the manufacturing of injection molding and extrusion systems. Milacron also produces and provides machinery, auxiliaries and components that complement its plastics processing machines and systems. The company’s 1,900 associates worldwide collaborate to provide a diverse range of products across various plastics applications in industries such as automotive, construction, medical, telecommunications, material handling, packaging, and much more. Milacron holds longstanding relationships with more than 27,000 global customers across North America and India, as well as coverage in Europe and in many emerging markets, including Central/South America. Milacron is an Operating Company of Hillenbrand (NYSE: HI), an industrial company operating in over 100 countries serving a wide variety of industries across the world.
About Hillenbrand
Hillenbrand (NYSE: HI) is a global industrial company that provides highly-engineered, mission-critical processing equipment and solutions to customers in over 100 countries around the world. Our portfolio is composed of leading industrial brands that serve large, attractive end markets, including durable plastics, food, and recycling. Guided by our Purpose — Shape What Matters For Tomorrow™ — we pursue excellence, collaboration, and innovation to consistently shape solutions that best serve our associates, customers, communities, and other stakeholders. To learn more, visit www.Hillenbrand.com.
MEDIA CONTACTS
Bunlim Ly | Senior Director, Marketing
[email protected]
Geriann Taylor | Corporate Global Trade Show & Events Manager
[email protected]
IMAGES
The universal M-Series delivers greater versatility, reliability, and improved dry cycle time. The M-Series is driven by a servo motor hydraulic system that offers improved specifications and all-inclusive performance, as well as integrated control. In addition, faster clamp speeds, reliable tonnage assembly, and improved mold and eject access for quicker mold changes deliver optimal productivity and space savings.

The M-Series is a next-generation machine in Milacron’s fleet that showcases cutting-edge two-platen technology and exceptional efficiency, with the ability to integrate multiple co-injection technologies that can support customers’ sustainability demands.

The SG75 extrusion system features a new control, poly-olefin pipe heads, and advanced technology in single/twin screws and barrels. It’s a fully integrated package with all required downstream equipment including a vacuum tank, pullers, saws and much more. At the end of the line, a live cobot will perform demonstrations at the show.

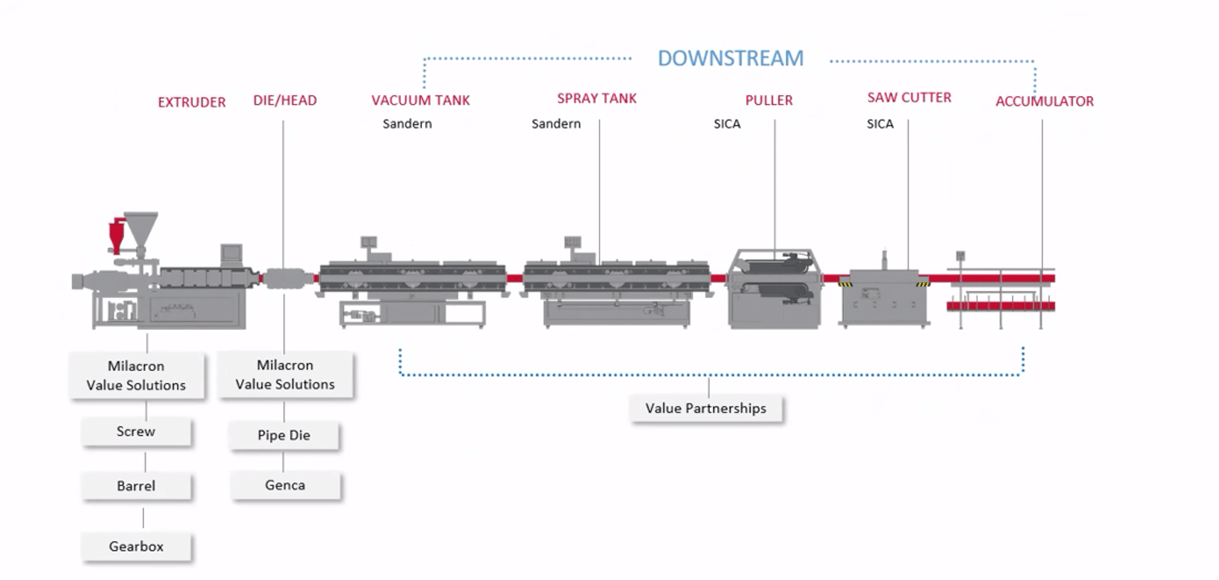
The new extrusion control fully integrates with all line components.
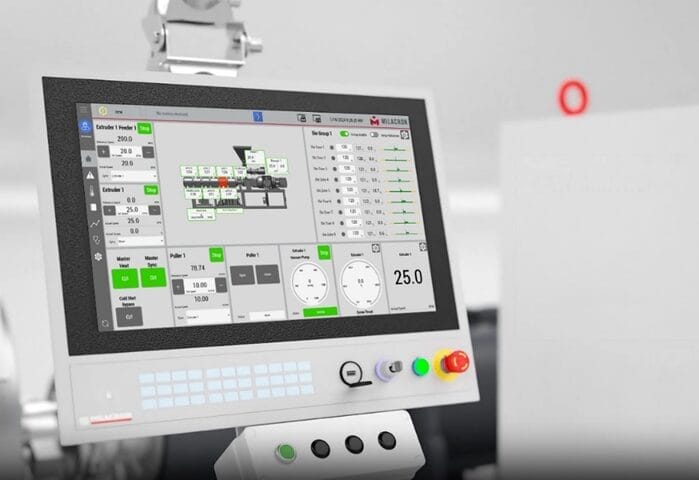
Milacron’s IIoT remote digital solution, M-Powered, leverages real-time machine data that provides unique insights on the plastic manufacturing process. With built-in analytics, the platform provides a clear picture of OEE and helps identify the root cause of downtime, quality issues, and production inefficiencies.
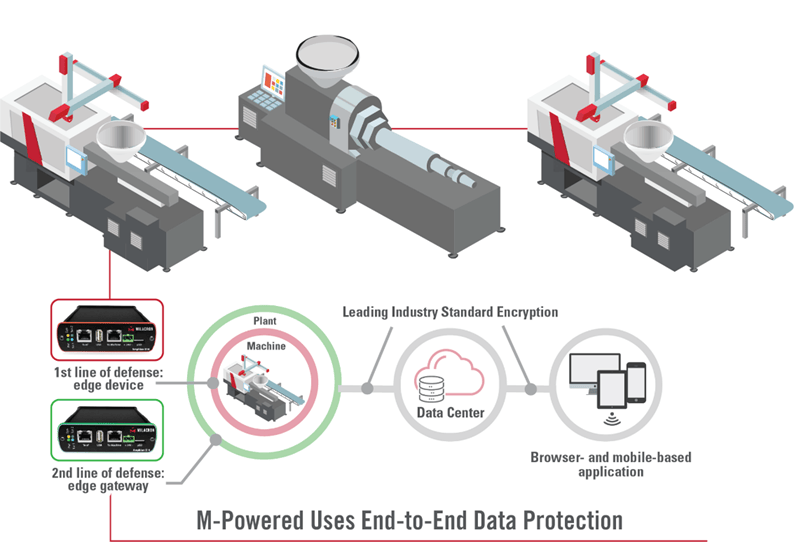
Plastics, Machinery & Manufacturing Magazine
The universal M-Series delivers greater versatility, reliability, and reduced dry cycle time.
[BATAVIA, OH] February 29, 2024 – The Milacron M-Series marks a new milestone in the OEM’s plastics processing system development. The two-platen machine impresses with clamping forces ranging from 506 tons to 1,236 tons, demonstrating its flexibility for a wide range of applications.
Inclusive of six models, the M-Series builds on the company’s proven machine technology and sets new standards for medium-tonnage solutions. Powered by best-in-class Fanuc motors and drives, the M-Series’ versatility and performance serve to meet the demanding needs of global industries – from automotive and consumer goods to packaging and customer molders.
The new injection molding machine line is driven by a servo motor hydraulic system that offers improved specifications and all-inclusive performance, as well as integrated control. In addition, faster clamp speeds, reliable tonnage assembly, and improved mold and eject access for quicker mold changes deliver optimal productivity and space savings. Features also include a mechanically synchronized nut lock design, with industry-leading tie-bar spacing.
The improved clamp design of the M-Series provides a greaseless part drop area, precise alignment, and increased access to the ejection plate. Its lower centerline promotes an ergonomic design allowing for improved access to mold area and ease of mold maintenance. Additionally, an injection swivel provides easy screw removal.
“The M-Series not only demonstrates outstanding performance potential for a wide range of applications but was designed with customer need in mind,” said Alec Woll, M-Series Product Manager for Milacron. “It’s a workhorse that’s built to perform with bigger molds in a more compact package, but with less energy consumption.”
The bi-directional hydraulic pump of the M-Series is engineered for rapid pressure control while operating at a lower maintenance cost. The closed-loop system also improves cycle precision and repeatability. Leveraging the servo motors in combination with hydraulic components gives the M-Series exceptional repeatability compared to induction motor machines.
Energy savings and sustainability are at the forefront of this new Milacron offering that touts reduced dry cycle time, power consumption and less lubrication requirements. Additionally, all presses are compatible with the M-powered IIoT solution – a user-friendly, observational, analytical remote support service that delivers quality data/insights, improved production, decreased downtime, and increased profitability. Milacron integrates M-Powered onto all its new machines, including the M-Series, for free for the first 12 months of ownership.
“The M-Series was developed with customer needs as a baseline,“ said Woll. “Not only is it versatile and compact, but it can be used with a wide selection of injection unit sizes, barrels, and screws. It’s the epitome of an all-inclusive injection molding solution for a wide range of processors.”
Milacron will showcase the new M-Series at NPE2024 in Orlando this May at booth W1601.
Learn more about the advantages of the new Milacron M-Series in this short video rendering.
About Milacron
Milacron (www.milacron.com) is a global industry and technology leader in the manufacture of injection molding and extrusion systems. Milacron also manufactures and supplies machines, auxiliaries and components that complement its plastics processing machines and systems. The company’s 1,900 employees worldwide collaborate to provide a wide range of products for various plastics applications in industries such as automotive, construction, medical, telecommunications, material handling, packaging and many more. Milacron has long-standing relationships with more than 27,000 global customers in North America and India, as well as in Europe and many emerging markets, including Central and South America.
Milacron is an operating company of Hillenbrand Inc, an industrial company operating in over 100 countries and serving a variety of industries around the world. www.hillenbrand.com
CONTACT
Melanie Murray, Communications Specialist
[email protected] / 513.300.6020
Images
The universal M-Series delivers greater versatility, reliability, and reduced dry cycle time.
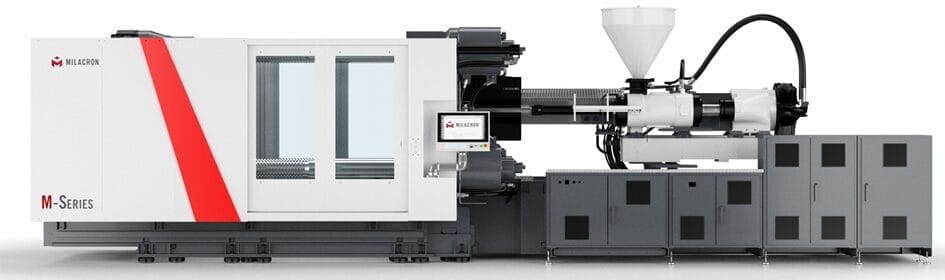
Clamp: Two-platen technology features rigid platen design with “open box” construction and reliable tonnage design.
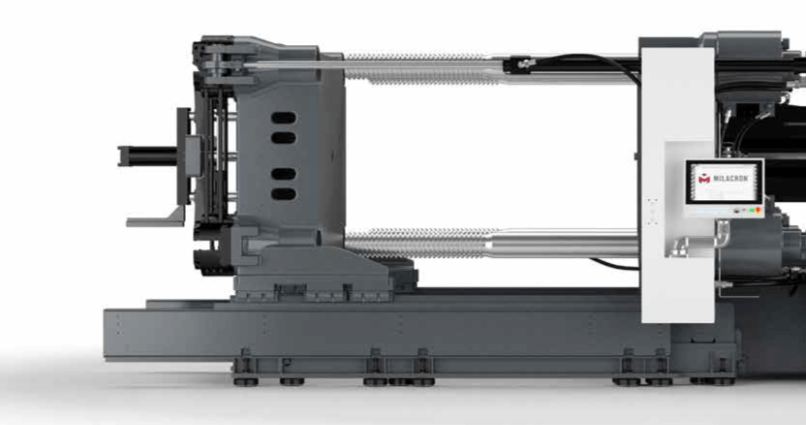
Through the years it’s been said our people, products, and legacy here at Milacron are something special- ask Steve Steward, a 35-year veteran of the company. He’s the third in a line of four generations, consisting of five family members, and more than 110 years of tenured service to the Southwest Ohio-based company.
When Steve was hired in Milacron assembly back in 1988, he signed a 20-year commitment within that division. Little did he know the journey his career would take with the company over the next more than three decades, including powerline machines in the old Oakley facility, several years as a specialist of the VH machine (a retired injection molding series), a season of extensive travel in the warranty service sector, facility and organizational transitions, as well as the birth of his twin sons that would also eventually carry on the family legacy for years to come.
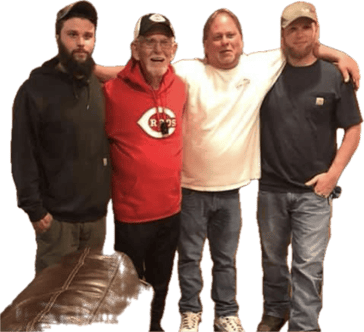
These days Steve works at Milacron’s global headquarters just outside Batavia, Ohio as a Customer Account Specialist in auxiliary parts, where he relies on his extensive 35 years of industry knowledge to help him effectively document and troubleshoot injection molding machines. It’s a vastly different role than the assembly gig that introduced him to Milacron alongside his dad and grandpa in the 80s.
Steve attributes his longevity at Milacron to that of his father’s 44-year commitment to the company. Tom Steward, Jr. started at the Milacron Oakley facility as a University of Cincinnati Engineering Co-Op in the late 60s, before transferring to the Purchasing division at Afton in 1971. Tom Jr. had his hands in many buckets (no pun intended) as the industry shifted and plastics processing continued to expand in the 80s and 90s, including the Contract Service division at the Mt. Orab facility, where he inevitably retired in 2000. His father, the first generation of Stewards employed by the company, actually joined Milacron later in life, spending ten years also in Mt. Orab as a machinist before retiring in the late 1980’s. The apple certainly didn’t fall far from the tree!
Fast-forward to 2024, and Steve’s twin sons, the fourth generation of Stewards at Milacron, proudly stand alongside dad – Dustin in Aftermarket Sales with 13 years of service, and Dylan in General Parts with a decade under his belt. They are confident Great Grandpa Steward would be proud, as well as in awe of the industry and technology trends of today’s Milacron, so much of which has been touched by a Steward for decades-on-end.
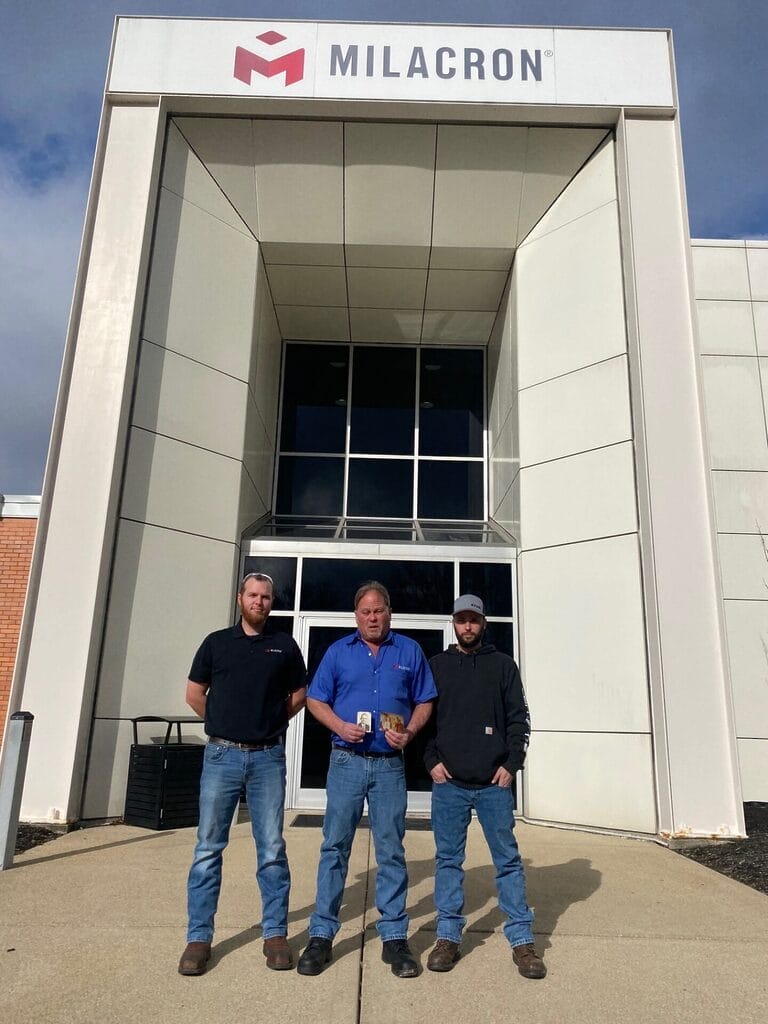
As for Steve, his 35-year tenure was celebrated during the company’s quarterly associate service award event at the end of 2023. And, although he currently enjoys the presence of his boys as co-workers at the Milacron headquarters facility, their drag racing weekends together are far more entertaining!
Cincinnati Business Courier
Bemis Manufacturing Company first turned to Milacron in the 1970s for machine solutions that produced a variety of plastics for its operations in both the consumer and commercial markets. From top-of-the-line household products like toilet seats, bidets, and faucets to healthcare solutions, after nearly fifty years in partnership, Milacron still delivers first-class innovation, technology, and service to the processor – a true lifecycle partnership in plastics.
One of their first collaborative advancements, Milacron and Bemis pioneered co-injection technology to improve part performance and cost, while minimizing cycle time and production volume. Eventually, co-injection would help integrate PCR (post-consumer recycled) into the plastics manufacturing process, offering a more sustainable alternative for processors today. The Bemis fleet of Milacron solutions includes a variety of high-pressure injection molding machines, co-injection, and digital control technologies.
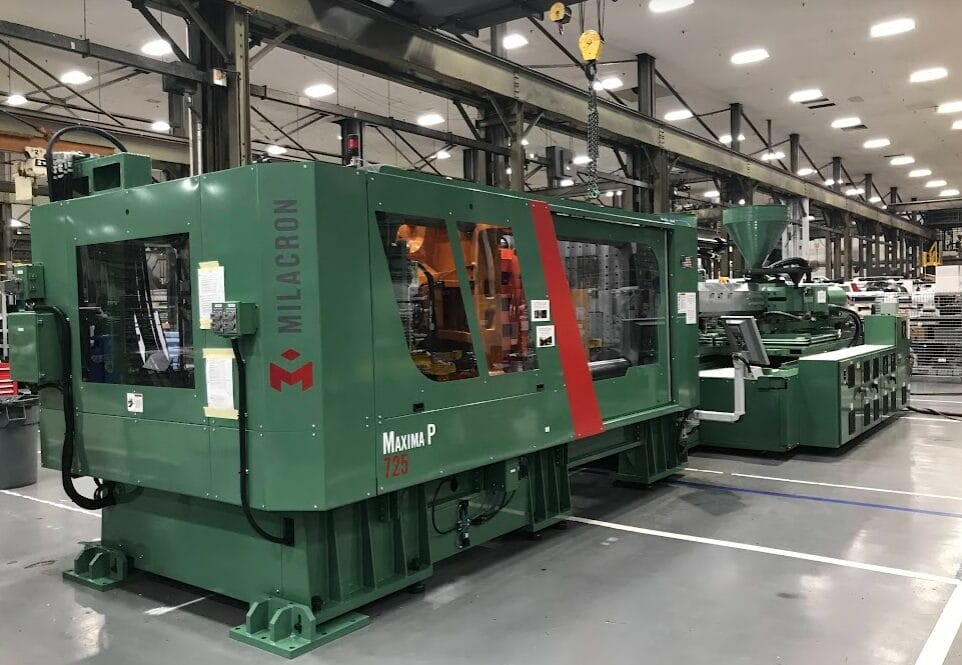
In recent years Bemis posed Milacron with the need for machine retrofits and digital upgrades in an effort to improve scrap rates and sustainability, as well as to save energy.
Today, Bemis manufactures products under its own brands and provides expertise to others, including private-label products and component parts for a variety of consumer, commercial, medical, and industrial markets in five countries around the world.
Milacron values the loyal partnership as the two companies continue to collaborate on advancements in plastics solutions that are groundbreaking and meet public demand.
#PartnerWithPossibility
Learn more about the solutions and possibilities this partnership has shaped.
Plastics Machinery & Manufacturing Magazine
Plastics Machinery & Manufacturing Magazine