A new universal injection molding platform, progressive co-injection technology, an 85-foot extruder line with live cobot demonstrations, in-mold foil decorations, exclusive IIoT digital solutions, and more on display this May.
[BATAVIA, OH] March 29, 2024 –Milacron®, a global leader in the manufacture, distribution, and service of highly engineered and customized systems within the plastic processing industry, will demonstrate advanced equipment solutions, innovative mold technologies, and comprehensive service and support systems at NPE May 6-10 in Orlando.
A pioneer in the plastics processing industry, and one of the largest North American-based OEMs, Milacron is set to showcase its latest advancements and innovative solutions, including the North American debut of its new M-Series IMM platform that features the largest clamp stroke available as standard in the mid-tonnage hybrid range within a compact footprint. Powered by industry-leading Fanuc motors and drives, the M-Series machines’ versatility and performance are designed to meet the demanding needs of global industries, from automotive and consumer goods to packaging and custom molders.
Booth W1601, the largest exhibit space at NPE 2024, is designed to offer attendees an array of plastics processing technologies. In addition to its M-Series machine line, Milacron’s showcase includes several work cells and industry-leading exhibits, alongside innovations from fellow Hillenbrand Operating Companies Coperion, DME, Herbold, Mold-Masters, and Rotex.
“Much has evolved in the plastics processing space since we were all last together at NPE 2018, including our integration into the Hillenbrand family of leading industrial brands,” said Mac Jones, Milacron President. “Our sizeable presence at NPE 2024 underscores Milacron’s drive to deliver solutions that Shape What Matters For Tomorrow™ in the plastics processing industry.”
Two different M-Series machine applications are planned for the booth. The M-1070, featuring Mold-Masters co-injection technology, is a two-cavity-mold pail application with up to 50% recycled core and includes IML (In-Mold Labeling) automation. The M-500 machine cell features a Mold-Masters hot runner and Kurz in-mold decoration technology for custom textures and backlit applications in global automotive and appliance applications.
The L-Series, Milacron’s LPIM platform, has been at the forefront of the low-pressure injection market for more than fifty years. Wide-range molding flexibility and part design are possible through nozzle sequencing. Most notably, the Milacron LPIM machine can run up to 100% regrind flake material, resulting in significant energy and resource savings. This commitment to sustainability offers a competitive advantage to customers in a world increasingly seeking to meet environmental compliance. Due to space constraints, the L-Series will not be featured at the show, but an in-booth animation loop will display the benefits of this industry-leading low-pressure IMM technology for large-part production in structural foam and structural web applications.
Several variations of Milacron’s durable, general-purpose, high-performance Q-Series platform will be present. The Q-Series features a double-toggle design that leverages a servo-hydraulic package delivering quality parts at a rapid pace while minimizing energy use. At the Milacron booth, the Q-170 machine displays a new G3 Mosaic control, DME mold technologies utilizing a bio-resin material, as well as custom ID/serialization and QR code stamping. A mobile phone holder will be the Q-170’s featured application. Additionally, Milacron’s Q-125 will be active in the Sepro booth (W143), where four private-labeled Sepro robots will integrate with the machine to produce a two-cavity mini disc.
The all-electric Fanuc Roboshot showcases two different applications within the booth that integrate DME Flosense water manifold technology. The Robo 55 features LSR (liquid silicon rubber) material and automation that is common in automotive, electrical, and medical applications. The cell includes a micro-plunger to precisely control small-capacity volume for the umbrella part produced that requires a tiny shot. Also in the booth, the Robo 275 machine cell shows a 48-cavity medical vial application. Partnering Operating Company, Mold-Masters, displays its new M3 thermocouple technology in this machine, ensuring precise temperature measurement in its Master-Series Pico hot runner with the Accu-Valve MX gate system. An added solution to this cell that makes it ideal for processors requiring a clean room environment, Milacron’s stainless steel water system is also featured on the Robo 275.At the far end of the cell, a platen-mounted robot with a conveyor retrieves the small plastic parts and places them in bins in a space-saving envelope containment area.
Milacron’s SG-75 extrusion pipeline exhibit can’t be missed, spanning more than 85 feet long, with an exclusive new control that fully integrates all line components. Additional features include the gravimetric feeder system, new polyolefin pipe heads, the latest technology in single/twin screws and barrels, dynamic downstream equipment, and post-production automation. Attendees can view an articulating 6-axis cobot technology at work through live demonstrations.
Lastly, show participants can interact with Milacron’s M-Powered digital IIoT solution. A portfolio of easy-to-use observational, analytical, and support services that provide customers with a competitive advantage, improved OEE, and reduced scrap rates, M-Powered leverages IIoT technology through sophisticated algorithms that utilize real-time machine learning to monitor machine operations. Milacron integrates M-Powered onto all its new machines in the U.S. and Europe for free for the first 12 months of ownership.
An innovative world leader in plastic processing, Milacron delivers the next generation of manufacturing technology this May for a wide array of industries. From a new IMM platform in the mid-tonnage range to the largest extrusion line the company has ever exhibited, Milacron partners at NPE 2024 with fellow Hillenbrand Operating Companies, as well as some of the top plastics processing partners in the industry, to Shape What Matters For Tomorrow.
About Milacron
Milacron (www.milacron.com) is a global industry and technology leader in the manufacturing of injection molding and extrusion systems. Milacron also produces and provides machinery, auxiliaries and components that complement its plastics processing machines and systems. The company’s 1,900 associates worldwide collaborate to provide a diverse range of products across various plastics applications in industries such as automotive, construction, medical, telecommunications, material handling, packaging, and much more. Milacron holds longstanding relationships with more than 27,000 global customers across North America and India, as well as coverage in Europe and in many emerging markets, including Central/South America. Milacron is an Operating Company of Hillenbrand (NYSE: HI), an industrial company operating in over 100 countries serving a wide variety of industries across the world.
About Hillenbrand
Hillenbrand (NYSE: HI) is a global industrial company that provides highly-engineered, mission-critical processing equipment and solutions to customers in over 100 countries around the world. Our portfolio is composed of leading industrial brands that serve large, attractive end markets, including durable plastics, food, and recycling. Guided by our Purpose — Shape What Matters For Tomorrow™ — we pursue excellence, collaboration, and innovation to consistently shape solutions that best serve our associates, customers, communities, and other stakeholders. To learn more, visit www.Hillenbrand.com.
MEDIA CONTACTS
Bunlim Ly | Senior Director, Marketing
[email protected]
Geriann Taylor | Corporate Global Trade Show & Events Manager
[email protected]
IMAGES
The universal M-Series delivers greater versatility, reliability, and improved dry cycle time. The M-Series is driven by a servo motor hydraulic system that offers improved specifications and all-inclusive performance, as well as integrated control. In addition, faster clamp speeds, reliable tonnage assembly, and improved mold and eject access for quicker mold changes deliver optimal productivity and space savings.

The M-Series is a next-generation machine in Milacron’s fleet that showcases cutting-edge two-platen technology and exceptional efficiency, with the ability to integrate multiple co-injection technologies that can support customers’ sustainability demands.

The SG75 extrusion system features a new control, poly-olefin pipe heads, and advanced technology in single/twin screws and barrels. It’s a fully integrated package with all required downstream equipment including a vacuum tank, pullers, saws and much more. At the end of the line, a live cobot will perform demonstrations at the show.

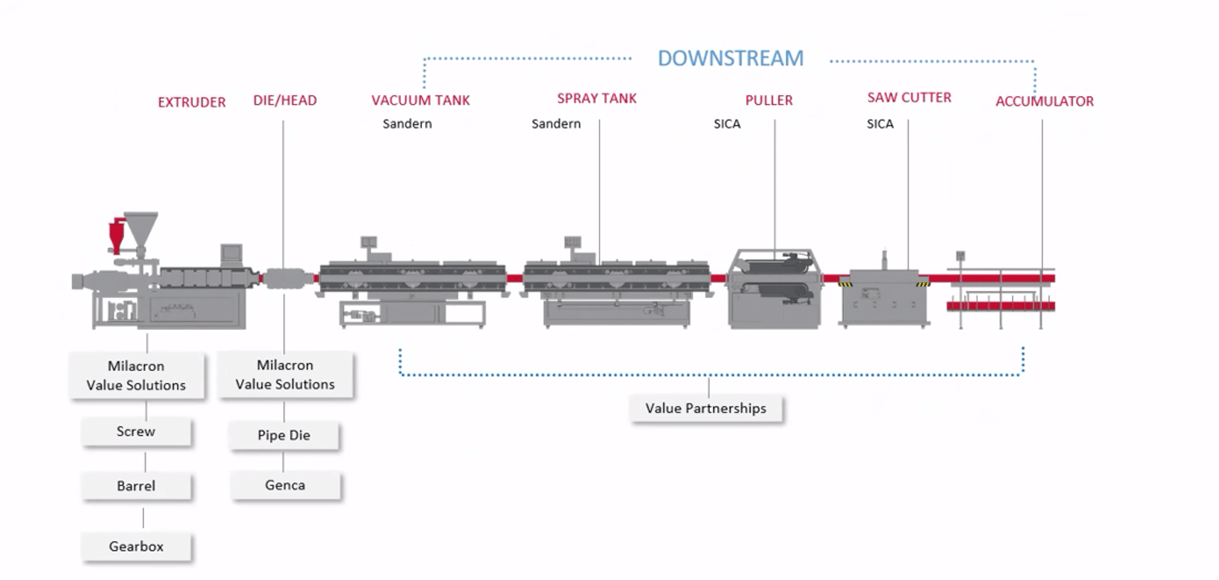
The new extrusion control fully integrates with all line components.
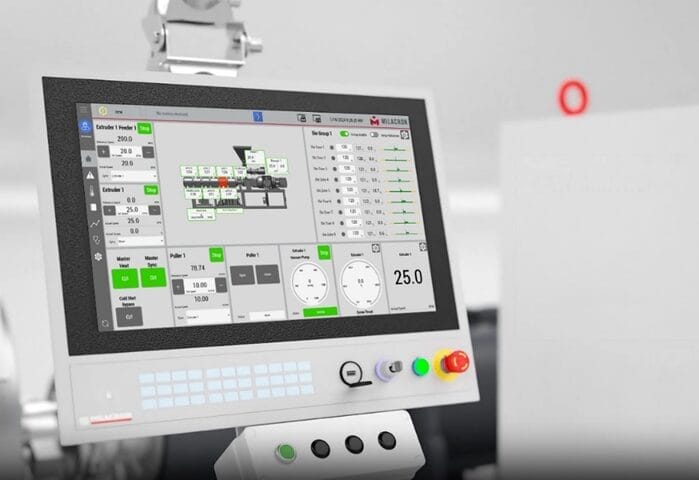
Milacron’s IIoT remote digital solution, M-Powered, leverages real-time machine data that provides unique insights on the plastic manufacturing process. With built-in analytics, the platform provides a clear picture of OEE and helps identify the root cause of downtime, quality issues, and production inefficiencies.
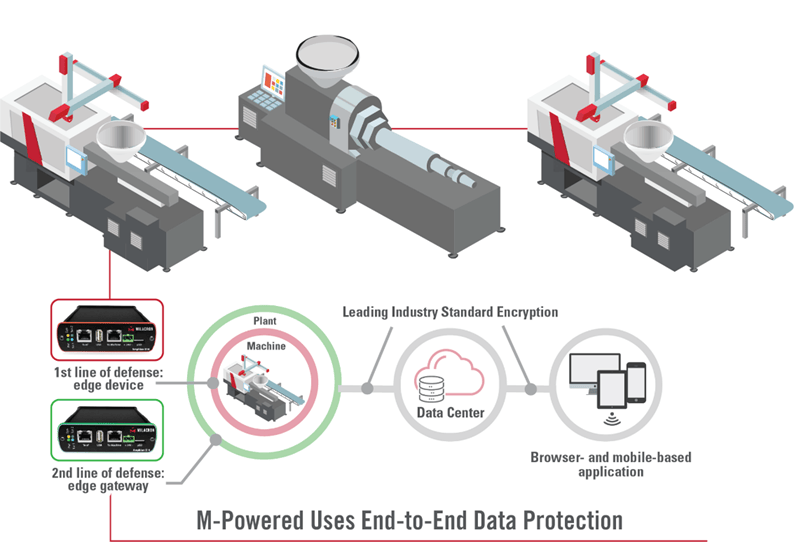
Plastics, Machinery & Manufacturing Magazine
Through the years it’s been said our people, products, and legacy here at Milacron are something special- ask Steve Steward, a 35-year veteran of the company. He’s the third in a line of four generations, consisting of five family members, and more than 110 years of tenured service to the Southwest Ohio-based company.
When Steve was hired in Milacron assembly back in 1988, he signed a 20-year commitment within that division. Little did he know the journey his career would take with the company over the next more than three decades, including powerline machines in the old Oakley facility, several years as a specialist of the VH machine (a retired injection molding series), a season of extensive travel in the warranty service sector, facility and organizational transitions, as well as the birth of his twin sons that would also eventually carry on the family legacy for years to come.
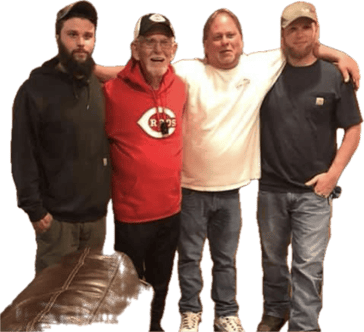
These days Steve works at Milacron’s global headquarters just outside Batavia, Ohio as a Customer Account Specialist in auxiliary parts, where he relies on his extensive 35 years of industry knowledge to help him effectively document and troubleshoot injection molding machines. It’s a vastly different role than the assembly gig that introduced him to Milacron alongside his dad and grandpa in the 80s.
Steve attributes his longevity at Milacron to that of his father’s 44-year commitment to the company. Tom Steward, Jr. started at the Milacron Oakley facility as a University of Cincinnati Engineering Co-Op in the late 60s, before transferring to the Purchasing division at Afton in 1971. Tom Jr. had his hands in many buckets (no pun intended) as the industry shifted and plastics processing continued to expand in the 80s and 90s, including the Contract Service division at the Mt. Orab facility, where he inevitably retired in 2000. His father, the first generation of Stewards employed by the company, actually joined Milacron later in life, spending ten years also in Mt. Orab as a machinist before retiring in the late 1980’s. The apple certainly didn’t fall far from the tree!
Fast-forward to 2024, and Steve’s twin sons, the fourth generation of Stewards at Milacron, proudly stand alongside dad – Dustin in Aftermarket Sales with 13 years of service, and Dylan in General Parts with a decade under his belt. They are confident Great Grandpa Steward would be proud, as well as in awe of the industry and technology trends of today’s Milacron, so much of which has been touched by a Steward for decades-on-end.
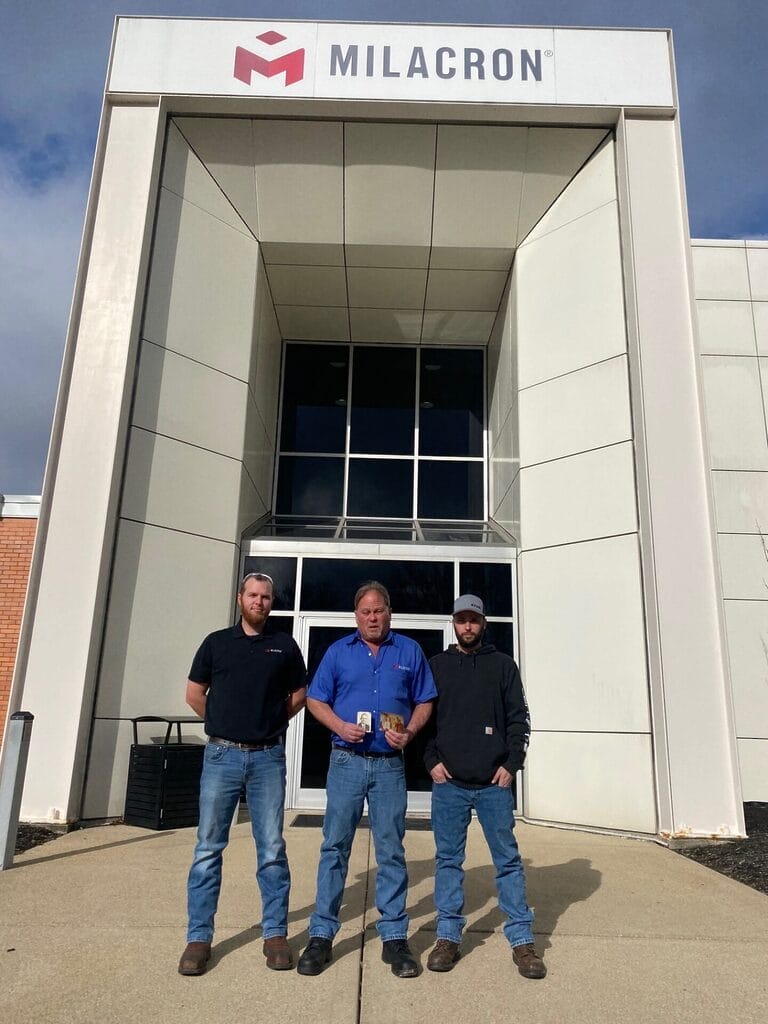
As for Steve, his 35-year tenure was celebrated during the company’s quarterly associate service award event at the end of 2023. And, although he currently enjoys the presence of his boys as co-workers at the Milacron headquarters facility, their drag racing weekends together are far more entertaining!
Cincinnati Business Courier
Bemis Manufacturing Company first turned to Milacron in the 1970s for machine solutions that produced a variety of plastics for its operations in both the consumer and commercial markets. From top-of-the-line household products like toilet seats, bidets, and faucets to healthcare solutions, after nearly fifty years in partnership, Milacron still delivers first-class innovation, technology, and service to the processor – a true lifecycle partnership in plastics.
One of their first collaborative advancements, Milacron and Bemis pioneered co-injection technology to improve part performance and cost, while minimizing cycle time and production volume. Eventually, co-injection would help integrate PCR (post-consumer recycled) into the plastics manufacturing process, offering a more sustainable alternative for processors today. The Bemis fleet of Milacron solutions includes a variety of high-pressure injection molding machines, co-injection, and digital control technologies.
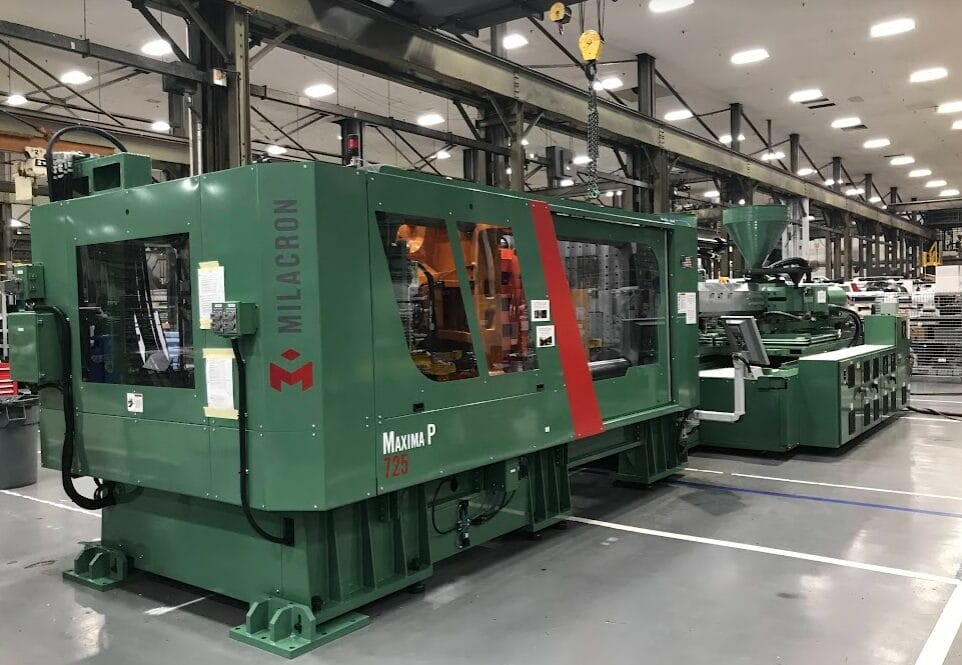
In recent years Bemis posed Milacron with the need for machine retrofits and digital upgrades in an effort to improve scrap rates and sustainability, as well as to save energy.
Today, Bemis manufactures products under its own brands and provides expertise to others, including private-label products and component parts for a variety of consumer, commercial, medical, and industrial markets in five countries around the world.
Milacron values the loyal partnership as the two companies continue to collaborate on advancements in plastics solutions that are groundbreaking and meet public demand.
#PartnerWithPossibility
Learn more about the solutions and possibilities this partnership has shaped.
Plastics Machinery & Manufacturing Magazine
Plastics Machinery & Manufacturing Magazine
Plastics News
Plastics Machinery & Manufacturing Magazine
The medical plastics market is an industry that relies on comprehensive manufacturing solutions to meet precise production requirements. Milacron’s cutting-edge Roboshot solutions are designed to meet these high demands with clean-room-ready machines and processes that produce consistent part quality.
The Roboshot’s gold-standard features, like configurable core sequence, flexible I/O, unmatched pressure control, and industry-leading artificial intelligence (AI) keep processors in the medical industry running with tight tolerances and precision year after year.
Milacron’s Roboshot customers are often loyal, as the machine is known worldwide for best-in-class reliability. Elite Biomedical Solutions, a Milacron customer for more than a decade, produces replacement components for infusion and telemetry assets for hospital biomed departments across the United States. Being in healthcare, Elite requires a machine solution that consistently produces with precision, day-in-and-day-out.
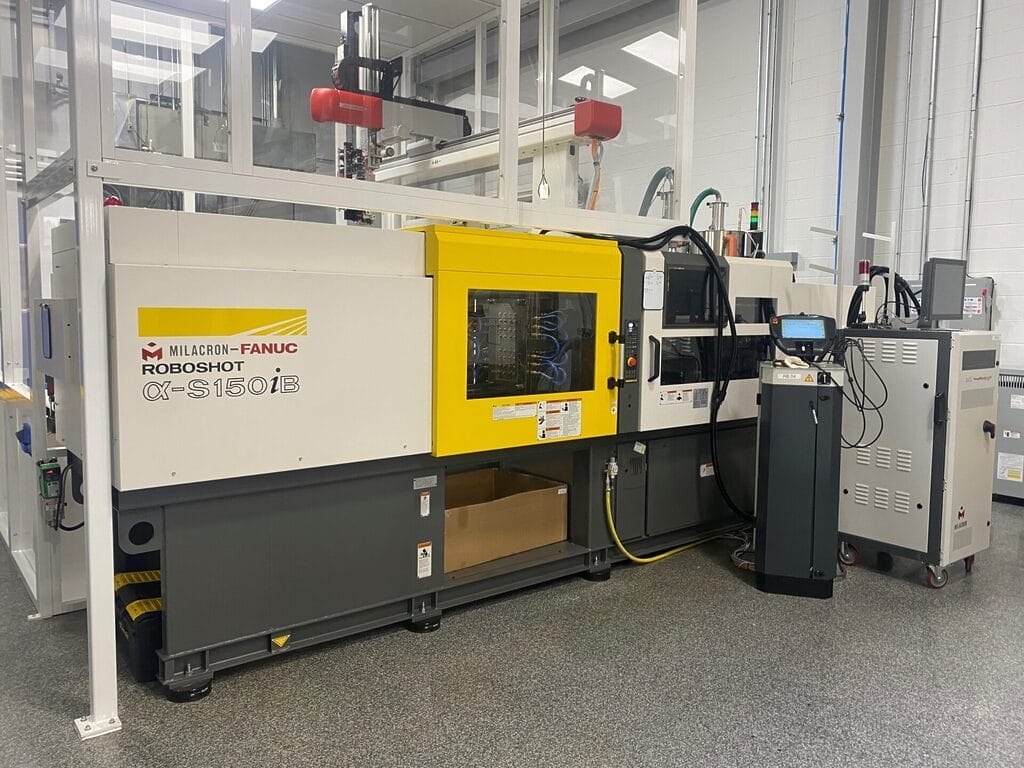
“Typically we run low volumes, but very tight tolerances, and that’s healthcare,” explains Elite CEO and Founder, Jeff Smith. “As a result of that, with the Roboshot solution, we’re guaranteed that process to be consistent with every part we make, and we make thousands and thousands of parts weekly.”
Elite Biomedical is a Milacron-only house of five Roboshots that are flanked with various pieces of Milacron auxiliary equipment to support. A company that got its start in the basement of CEO, Jeff Smith’s home nearly a decade ago, Elite has grown to a multi-million-dollar business in a short period of time. The growth has even allowed the company to branch off with its own custom contract manufacturing segment, Elite Precision Plastics.
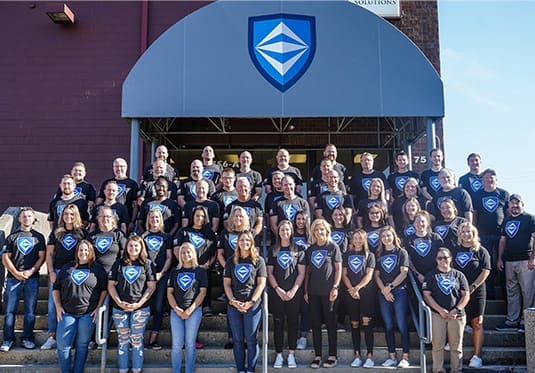
Smith attributes the success of his dynamic business to not just the reliability of his Roboshot fleet, but the ease of working with Milacron through the years for all his company’s plastics processing needs.
“We do all of our shopping with Milacron and get all our accessory equipment through them and their partnerships,” he said. “They’ve been very consistent. Their training is all the same. And, who’s going to take care of us is all the same. It brings a sense of security and peace of mind, which is important to me as CEO.”
Learn more about Elite Biomedical’s fleet of Roboshots and the partnership they’ve come to rely upon with Milacron over the last decade in this short Partner With Possibility success story video . For a deeper product dive on the Roboshot machine, check out the Roboshot landing page, where a full product brochure can be downloaded. And, for additional product expertise, Milacron’s Kent Royer, Sr. Product Manager for the Roboshot, can be found on LinkedIn, as well as in-person at NPE 2024 at the Milacron booth, W1601, next May.